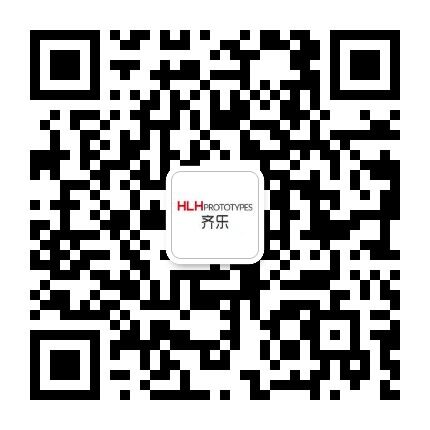
微信客服

在线客服
数控加工经验
发布时间:2025年02月11日
数控加工经验是宝贵的财富,它们涵盖了从工艺规划到实际操作的各个环节。以下是一些关键的数控加工经验:
工序划分与加工顺序
刀具集中分序法:按所用刀具划分工序,用同一把刀加工完零件上所有可以完成的部位,再换刀依次加工其他部位,可减少换刀次数,压缩空程时间,减少不必要的定位误差。
加工部位分序法:对于加工内容很多的零件,可按其结构特点将加工部分分成几个部分,如内形、外形、曲面或平面等。一般先加工平面、定位面,后加工孔;先加工简单的几何形状,再加工复杂的几何形状;先加工精度较低的部位,再加工精度要求较高的部位。
粗精加工分序法:对于易发生加工变形的零件,由于粗加工后可能发生的变形而需要进行校形,故一般来说凡要进行粗、精加工的都要将工序分开。
工件装夹
力求设计、工艺、与编程计算的基准统一,以减少因基准不统一而产生的误差。
尽量减少装夹次数,尽可能做到在一次定位后就能加工出全部待加工表面,以提高加工效率和保证加工精度。
避免采用占机人工调整方案,以免影响加工的稳定性和精度。
夹具要开畅,其定位、夹紧机构不能影响加工中的走刀,碰到此类情况时,可采用虎钳或加底板抽螺丝的方式装夹。
对刀与坐标系设定
对刀点可以设在被加工零件的上,但注意对刀点必须是基准位或已精加工过的部位,且在第一道工序对刀时注意要在与定位基准有相对固定尺寸关系的地方设立一个相对对刀位置,这样便于后续根据它们之间的相对位置关系找回原对刀点。
工件坐标系的原点位置是由操作者自己设定的,它反映的是工件与机床零点之间的距离位置关系,工件坐标系一旦固定,一般不作改变,且工件坐标系与编程坐标系两者必须统一。
走刀路线规划
保证零件的加工精度要求,合理规划刀具的运动轨迹和方向,避免多余的路径和动作。
方便数值计算,减少编程工作量,尽量选择简单的几何形状和易于计算的走刀路线。
寻求最短加工路线,减少空刀时间以提高加工效率,但也要注意不能与加工精度等要求相冲突。
确保工件轮廓表面加工后的粗糙度要求,最终轮廓应安排最后一走刀连续加工出来,并且要注意刀具的进退刀路线,尽量减少在轮廓处停刀而留下刀痕,也要避免在轮廓面上垂直下刀而划伤工件。
加工过程监控与调整
粗加工监控:主要考虑快速切除工件表面的多余余量,注意通过切削负荷表观察自动加工过程中的切削负荷变化情况,根据刀具的承受力状况,调整切削用量,发挥机床的最大效率。
切削声音监控:正常切削时声音稳定、连续、轻快,若出现不稳定、相互撞击声或机床震动等异常声音,应及时调整切削用量及切削条件,必要时暂停机床检查刀具及工件状况。
精加工监控:着重注意积屑瘤对加工表面的影响,对于型腔加工还要注意拐角处加工过切与让刀等问题。可通过调整切削液的喷淋位置、观察工件已加工面质量并调整切削用量等方式来解决。
刀具监控:通过声音监控、切削时间控制、切削过程中暂停检查、工件表面分析等方法判断刀具的正常磨损状况及非正常破损状况,并根据加工要求及时处理刀具,防止产生加工质量问题。
刀具选择与使用
根据不同的加工材料、加工要求和加工部位等因素选择合适的刀具类型、刀具材料和刀具规格。
合理确定切削用量,包括切削速度、进给量和背吃刀量等参数,以保证加工效率和加工质量。一般来说,当背吃刀量增大一倍时,切削力会增大一倍;进给率增大一倍时,切削力大概增大70%;切削速度增大一倍时,切削力逐渐减小。
注意刀具的磨损情况,及时更换磨损严重的刀具,以避免影响加工精度和表面质量。
总的来说,数控加工经验的积累对于提高加工效率和质量至关重要。通过不断优化工序划分、工件装夹、对刀与坐标系设定、走刀路线规划以及加强加工过程的监控与调整,可以显著提升数控加工的整体水平。
上一篇: 3d打印技巧有哪些
下一篇: 3d打印抛光注意事项