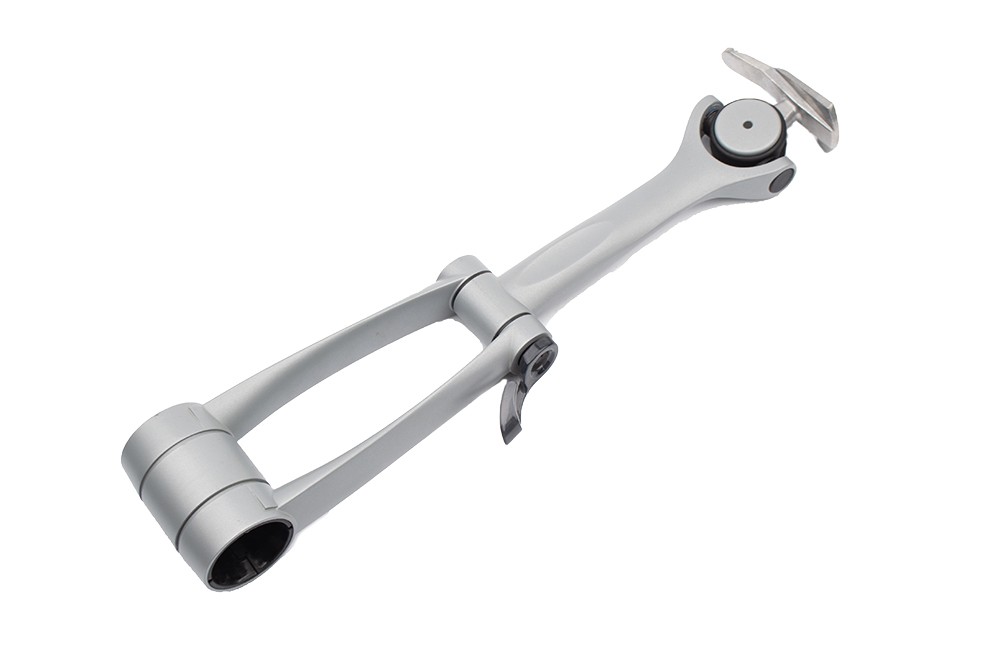
行业/分类:其他手板模型加工
加工方式: cnc加工 使用材料: 塑料
最小精度: 0.05mm 生产周期: 2~7天
产品尺寸: 30cm*8cm*3cm
后处理: 打磨
加工流程
设计阶段
创建3D模型:使用 SolidWorks、Autodesk Inventor 等专业3D建模软件,根据汽车中控塑料连接件的设计需求,精确创建三维模型,确定其尺寸、形状、结构和连接方式等细节。
设计评审:组织设计团队、工程人员和相关部门对3D模型进行评审,检查是否符合汽车整体设计要求、功能需求及制造工艺性,根据反馈意见进行修改优化。
编程阶段
导入模型与生成代码:将3D模型导入 Mastercam、Fusion 360 等 CAM 软件,生成 CNC 机床可识别的G代码,确定刀具路径、切削参数等。
程序校验:对生成的G代码进行模拟仿真,检查刀具路径是否正确,是否存在碰撞、过切等问题,确保程序的准确性和安全性。
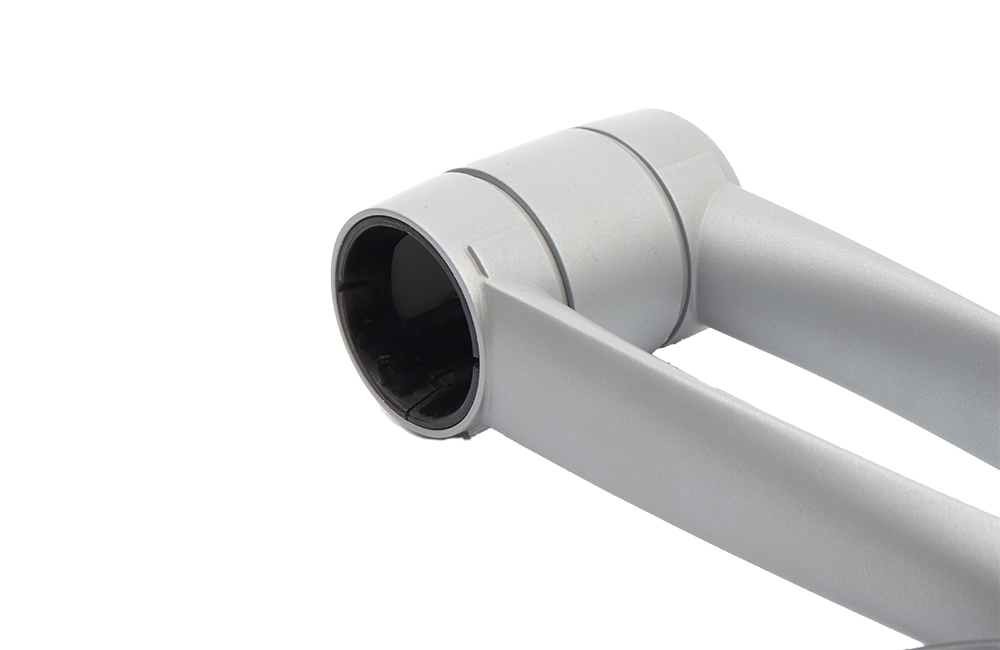
加工准备阶段
材料选择:根据连接件的性能要求,选择合适的塑料材料,如具有良好的强度、韧性和耐磨性的ABS、PC、尼龙等。
选择机床:依据手板的尺寸、复杂程度和加工精度要求,选择合适的CNC机床,如3轴、4轴或5轴机床。
装夹材料:将选好的塑料材料固定在机床工作台上,使用夹具确保材料装夹牢固、定位准确,防止加工过程中发生位移。
CNC 加工阶段
粗加工:采用较大的刀具和较高的进给速度,快速去除大部分多余的塑料材料,使工件接近最终形状,为精加工留0.5-1mm的加工余量。
精加工:更换较小的刀具,以较低的进给速度和较高的主轴转速进行精细切削,保证零件的尺寸精度、表面粗糙度和几何精度符合设计要求。

后处理阶段
清理毛刺:使用砂纸、锉刀等工具对加工后的手板进行手工清理,去除表面的毛刺、飞边和刀痕,使表面光滑。
表面处理:根据需要进行表面处理,如打磨、抛光、喷涂、丝印等,以提高手板的外观质量和质感,使其更接近真实产品。
质量检验阶段
尺寸测量:使用卡尺、千分尺、三坐标测量机等精密测量工具,对手板的关键尺寸进行测量,确保尺寸偏差在设计要求的公差范围内。
外观检查:通过目视检查手板表面是否有裂纹、划伤、气泡等缺陷,颜色和光泽是否均匀一致。
功能测试:将手板与汽车中控的其他相关部件进行装配测试,检查连接件的配合是否良好,是否能够实现预期的连接功能。
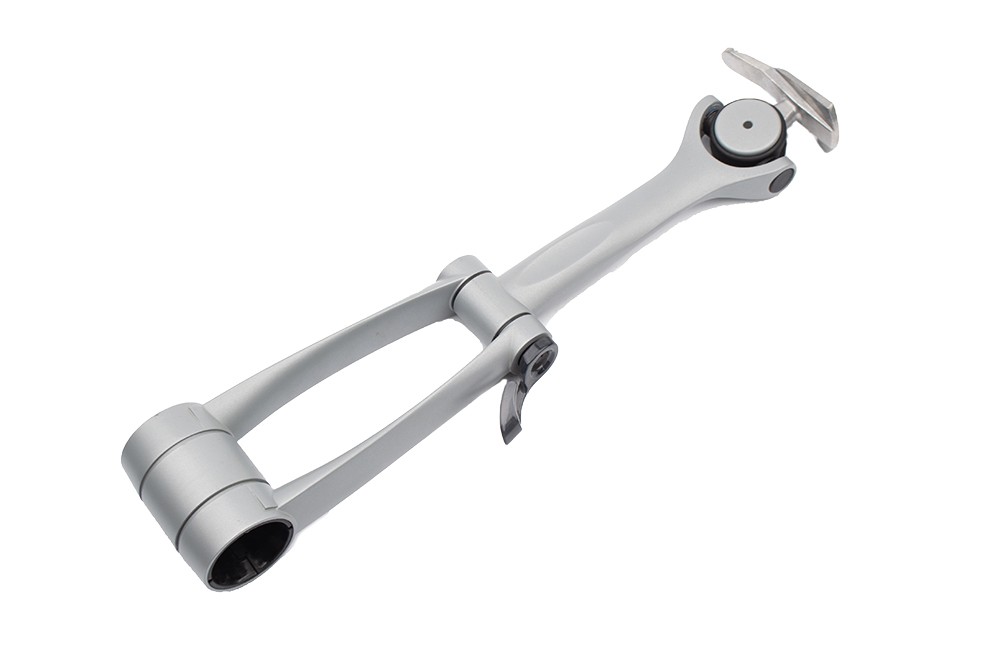
注意事项
材料特性:不同塑料材料有不同的加工特性,如ABS流动性好但韧性一般,PC韧性强但易产生内应力。要根据材料特性合理调整加工参数,如切削速度、进给量和切削深度等。
刀具选择:根据塑料材料的硬度、韧性和加工工艺要求,选择合适的刀具,如钨钢刀具适用于加工硬度较高的塑料,金刚石涂层刀具可提高切削效率和表面质量。
切削参数:切削参数直接影响加工效率和质量,参数选择不当可能导致材料过热、变形、表面质量差等问题。在加工前要通过试验或参考经验数据,确定合理的切削参数。
精度控制:汽车中控塑料连接件对手板的精度要求较高,要定期对CNC机床进行维护和校准,确保机床的精度和稳定性。在加工过程中,要严格控制装夹精度、刀具磨损和加工变形等因素。
环境温度:塑料材料的热膨胀系数较大,环境温度的变化可能会导致手板尺寸发生变化。在加工和测量过程中,要保持环境温度的稳定,尽量在恒温条件下进行。