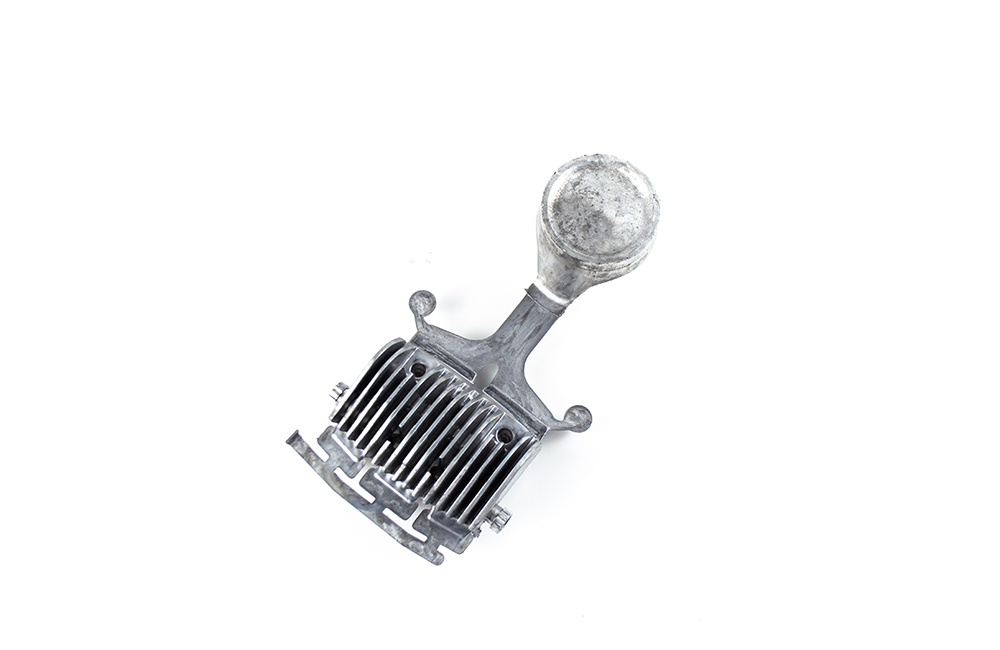
行业/分类:其他手板模型加工
加工方式: 钣金 使用材料: 铝合金
最小精度: 0.1mm 生产周期: 2~7天
产品尺寸: 15cm*5cm*4cm
后处理: 打磨
压铸加工是一种高效的金属成型工艺,在高速列车零件制造中发挥着重要作用,以下是关于压铸加工高速列车零件的详细介绍:
压铸加工原理及优势
压铸加工原理:压铸是将液态或半固态金属在高压作用下,以较高的速度填充压铸模具型腔,并在压力下凝固成型的一种精密铸造方法。
压铸加工优势:
高精度:能够制造出尺寸精度高、表面质量好的零件,减少了后续加工工序,提高生产效率,降低成本。
高强度:在高压下凝固成型,零件组织致密,力学性能好,能够满足高速列车对零件强度和可靠性的要求。
复杂形状成型能力:可以制造出形状复杂的零件,如带有薄壁、深腔、小孔等结构的零件,为高速列车零件的设计提供了更大的自由度。
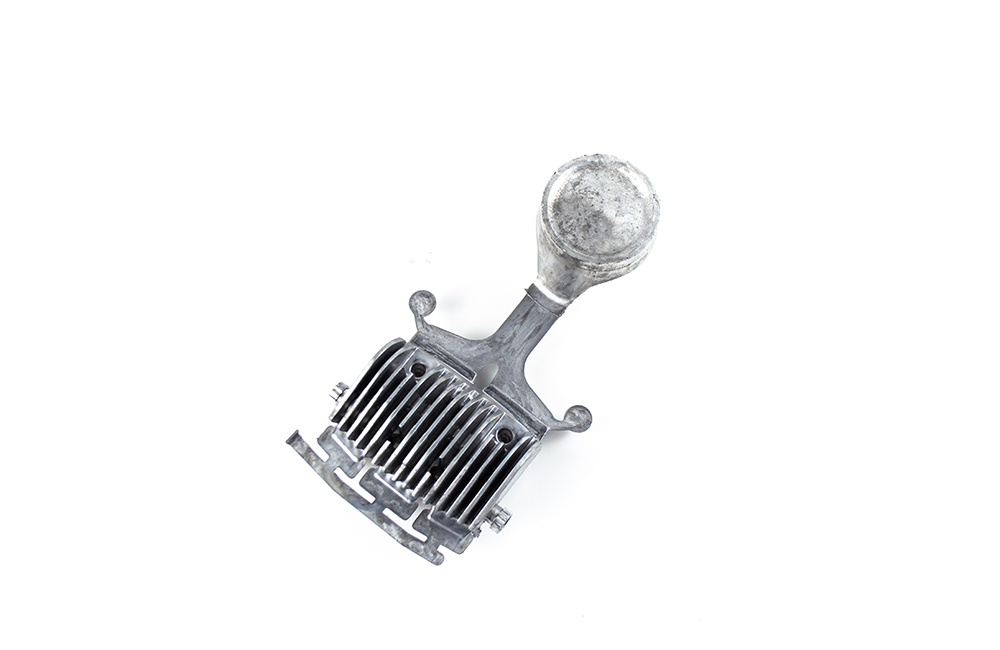
高速列车中常用压铸加工的零件
电机壳:电机是高速列车的核心部件之一,电机壳需要具备良好的散热性能、高强度和高精度。压铸加工的电机壳能够满足这些要求,并且可以实现复杂的散热结构设计,提高电机的散热效率。
齿轮箱箱体:齿轮箱是高速列车传动系统的重要组成部分,其箱体需要承受较大的载荷和振动。压铸加工的齿轮箱箱体具有较高的强度和刚度,能够保证齿轮箱的稳定运行。
制动盘:制动盘是高速列车制动系统的关键部件,需要具备良好的耐磨性、热稳定性和高强度。压铸加工的制动盘可以通过添加合金元素和优化工艺参数,提高其性能指标,满足高速列车制动的要求。
车身结构件:高速列车的车身结构件需要具备轻量化、高强度和良好的抗疲劳性能。压铸加工可以使用铝合金等轻质材料制造车身结构件,在保证强度的同时,减轻列车的重量,提高列车的运行速度和能效。
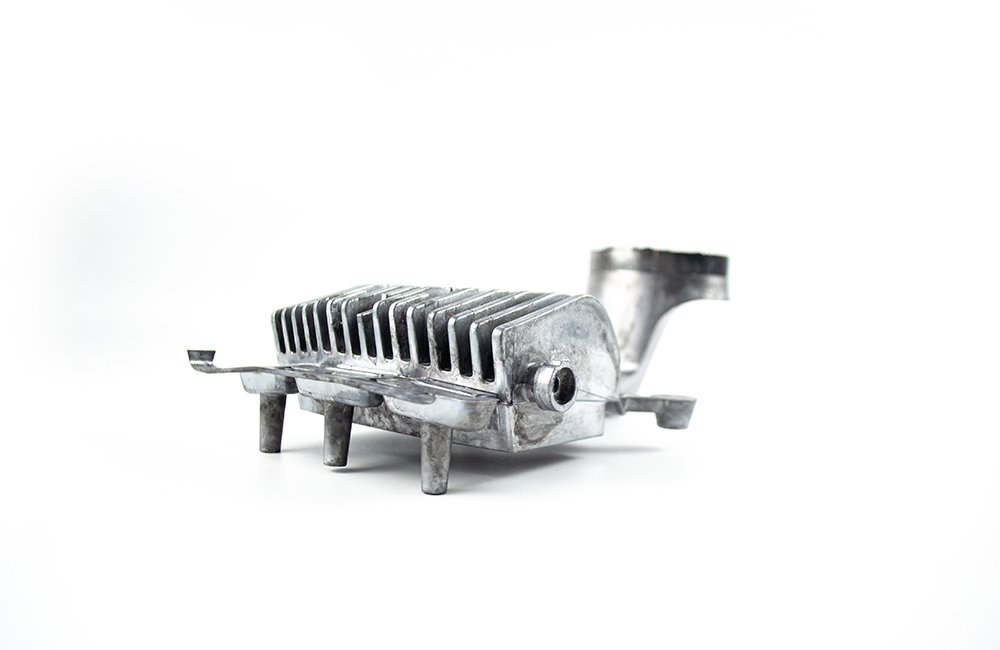
压铸加工工艺及设备
压铸工艺:包括模具设计、合金熔炼、压铸参数控制等环节。模具设计是压铸加工的关键,需要根据零件的形状、尺寸和性能要求,设计出合理的模具结构。合金熔炼需要严格控制合金成分和熔炼温度,以保证金属液的质量。压铸参数控制包括压力、速度、温度等参数的控制,需要根据不同的零件和合金材料,优化压铸参数,以获得良好的成型质量。
压铸设备:主要包括压铸机、熔炉、模具等。压铸机是压铸加工的核心设备,根据压力大小可分为冷室压铸机和热室压铸机。冷室压铸机适用于压铸熔点较高的合金材料,如铝合金、镁合金等;热室压铸机适用于压铸熔点较低的合金材料,如锌合金等。熔炉用于合金的熔炼和保温,模具则是压铸成型的关键工装。
压铸加工的质量控制
原材料检验:对压铸合金材料进行严格的检验,包括化学成分、力学性能、金相组织等方面的检查,确保原材料符合质量要求。
模具调试与维护:在压铸生产前,需要对模具进行调试,优化压铸参数,确保模具的成型质量。在生产过程中,需要定期对模具进行维护和保养,延长模具的使用寿命。
过程监控:采用先进的检测设备和技术,对压铸过程进行实时监控,包括金属液温度、压力、速度等参数的监测,及时发现和解决生产过程中的问题。
成品检验:对压铸成品进行全面的检验,包括尺寸精度、表面质量、力学性能等方面的检测,确保产品质量符合相关标准和客户要求。
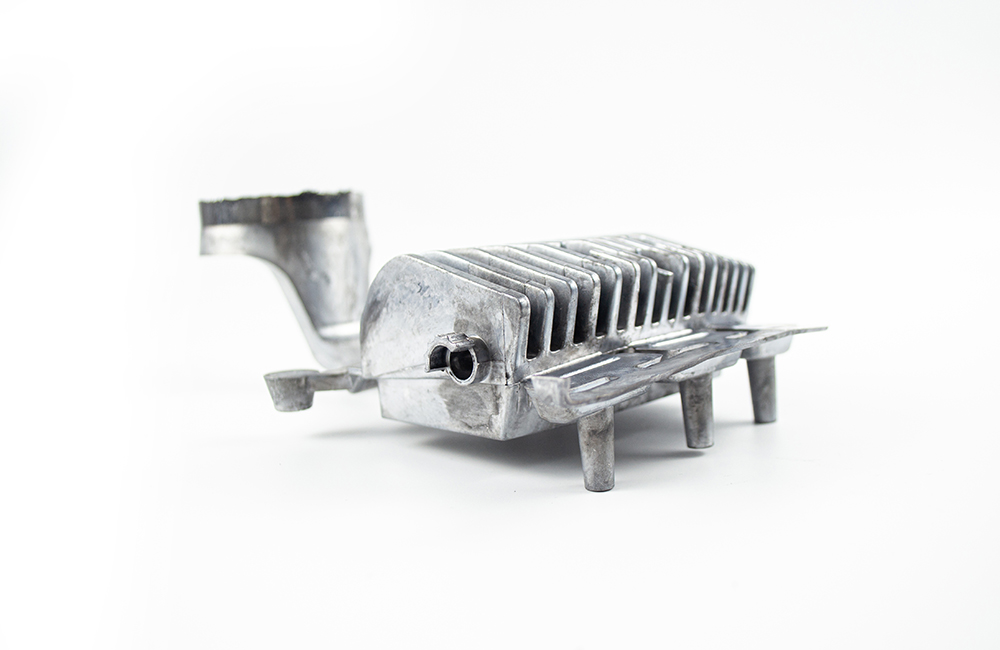
压铸加工的发展趋势
高性能合金材料的应用:随着高速列车对零件性能要求的不断提高,压铸加工将越来越多地应用高性能合金材料,如高强度铝合金、镁合金、钛合金等,以满足高速列车轻量化、高性能的发展需求。
先进压铸技术的发展:如真空压铸、半固态压铸、挤压压铸等先进压铸技术将得到更广泛的应用。这些技术能够进一步提高压铸零件的质量和性能,拓展压铸加工的应用范围。
智能化制造:借助于大数据、人工智能、物联网等技术,压铸加工将向智能化制造方向发展。通过实现压铸生产过程的自动化、智能化控制,提高生产效率、产品质量和企业的竞争力。
绿色环保:在环保政策日益严格的背景下,压铸加工将更加注重绿色环保。采用环保型的压铸工艺和设备,减少能源消耗和污染物排放,实现压铸行业的可持续发展。